Double Seaming Made Simple – Part 3
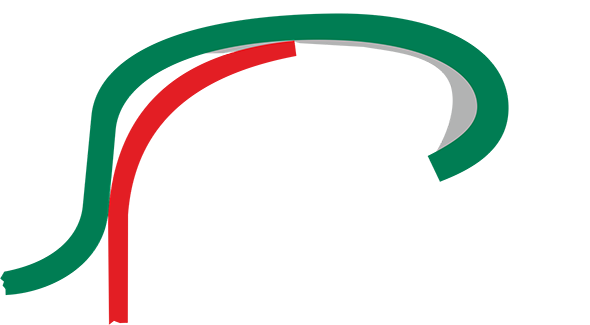
When it comes to metal cans, the ability to lock-in and preserve the freshness of ingredients, while also keeping out unwanted elements such as microorganisms and oxygen – is a big advantage. The double seam, found today on virtually all food and beverage cans is a simple and proven way to provide such a hermetic seal. In the following series, we’ll outline a few key steps will lend you a better sense of how to achieve a fault-free seal.
Tip Two: Recognize the Importance of the First Operation Seam
The importance of the first operation seam is frequently overlooked as it is difficult to access in most automated seamers, often requiring parts to be removed to stop the second operation being carried out. If, however, the first operation is not properly executed, it will be almost impossible to achieve a successful double seam. A fact to consider is that the first operation seam controls proper formation of the cover hook, which consequently controls the formation of the body hook as well as the depth of the countersink. A helpful tip is to closely follow the can manufacturer’s standards for determining suitable tolerances for flange and end thicknesses, can diameter, countersink and tooling profiles.
Tip Three: Check the First Operation
If you are experiencing trouble with the first operation, you’ll need to carefully examine the seam according to the following guidelines. (Note: As a precaution, be sure that the second operation seam is backed off or changed to the off-seam position prior to inspecting the first operation). Appropriate times to check the first operation seam are during the initial set-up of a seamer, while installing new seaming rolls and during the re-adjustment.